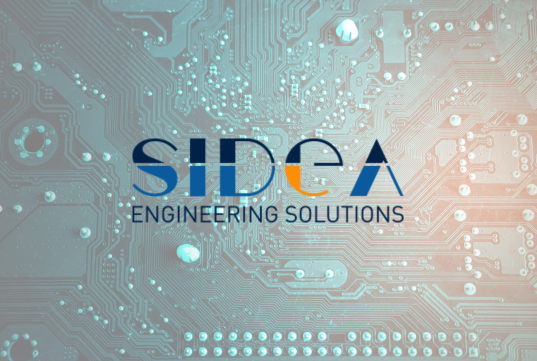
What are ATE systems, how does electronic board testing work?
Automatic Test Equipment or ATE systems are specialized devices used to perform electronic board testing. ATE systems are used in a wide range of applications, including the electronics industry, the automotive industry, the aviation industry, and other areas that use electronic boards. SIDeA designs automatic electronic board test systems to test a wide range of components, including, to give examples, microprocessors, integrated circuits, printed circuit boards, memories, signal converters, and sensors.
Automatic Test Equipment for Electronic Boards: an in-depth study
A fundamental stage in any manufacturing sector, testing has particular importance in the electronic board assembly sector. The testing phase here must be performed with extreme care to verify that each board meets the necessary specifications and performs the operations for which it was programmed. It is an integral part of electronic board fabrication in its own right and is intended to assess the quality of a board from an electronic and functional aspect. ATE systems designed by SIDeA use advanced techniques, such as functional testing, boundary scan testing, continuity testing, and other methods to detect malfunctions in components.
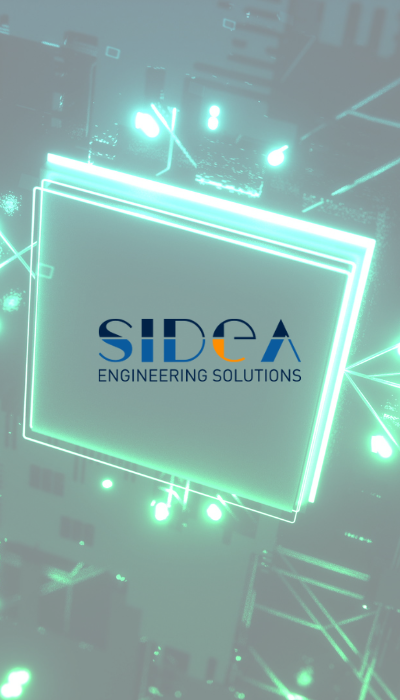
Electronic board testing: boundary scan testing combined with functional testing
Electronic board testing includes several steps aimed at evaluating the behavior and performance capability of electronic boards. The testing of medium-complex boards at the end of production has historically consisted of ICT testing followed by functional testing. The increasing complexity of digital electronic components, however, has made the Boundary Scan interface increasingly present, which is available on all state-of-the-art digital components such as FPGAs, microcontrollers, RAM, and converters.
As provided by the IEEE 1149.x JTAG standard, Boundary Scan involves circuitry within chips that makes available a complete board-level test protocol. Appropriately implemented by chip vendors, the aforementioned circuitry involves replacing physical probes (probes) with Boundary Scan - BSC cells. They simulate virtual probes for each input and output on the chip and each allows the user to:
- observe the usual flow of data through the I/O pins
- check the pin status through the serial communication of the Boundary chain.
The Boundary Scan test makes it possible to verify:
- the proper interconnection of all components, such as the absence of short circuits between tracks and verification of continuity
- the presence of many components while not being able to verify their exact value.
However, it cannot completely test all circuits on an electronic board, such as analog parts or all components without a Boundary interface. For this very reason, association with a functional test is indispensable. Indeed, this will allow to complete the testing of the system in all parts uncovered by the Boundary Scan and to perform the actual functional test.
The integrated Boundary Scan/Functional Test approach thus allows:
- have a dual type of test in a single device
- improve the test itself, which becomes more reliable
- have total coverage of all circuits in the Dut and all nets
- boast shorter test times
- improve insystem programming performance
- achieve better and more accurate fault diagnostics with unique reporting.
SIDeA: by each customer's side with design and development solutions for automatic electronic board testing
From analyzing and understanding the problem, evaluating the feasibility of interventions, each customer is followed and supported by SIDeA engineers during each phase. At the time of designing systems for automatic electronic board testing and their subsequent development, SIDeA's commitment does not end with the delivery of the required solutions. In fact, the phase following implementation is that of training, as well as technical support, tutoring, assistance and maintenance to optimize the systems and their use by the customer himself.
A heterogeneous and flexible work team, capable of managing the workload based on the professionalism and skills of each collaborator, guarantees a production flow that can carefully and accurately meet the established delivery deadlines.