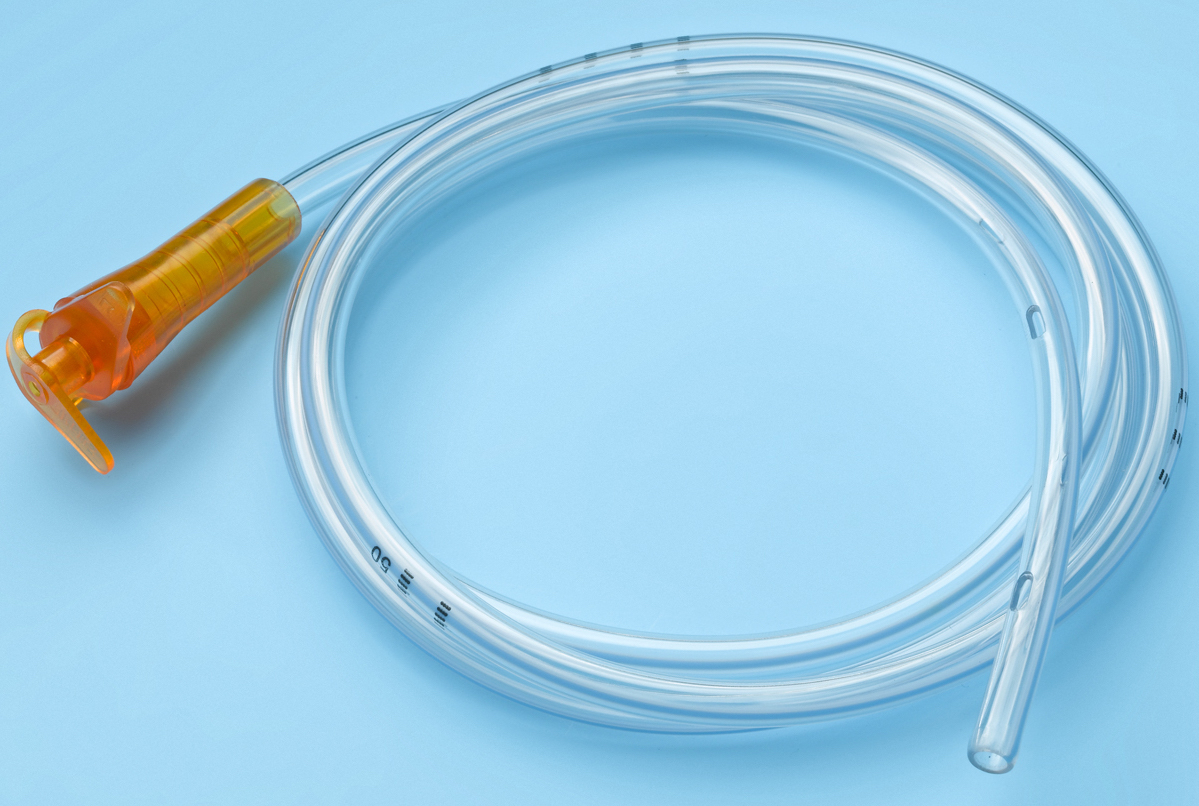
Latest technological advancements, including high-resolution scanners and compact laser-based systems have enhanced precision in quality control for the production of small-diameter polymeric tubes, meeting the industry's strictest standards
Producing small-diameter polymer tubes with strict dimensional tolerances is a significant challenge. To meet quality standards, cutting-edge extrusion equipment and advanced in-line monitoring systems are essential. In this article, we explore recent technological breakthroughs that have transformed dimensional measurement and control systems.
Key factors such as resolution, scanner light source, and scanning frequency have been critical for tube manufacturers. High scanning speed ensures that measurements remain unaffected by product movement or positioning as it traverses the testing field. Dual-plane scanners with a measurement field of up to 100 mm can now provide sub-micron repeatability by scanning thousands of times per second per plane. For applications requiring precise ovality control, two staggered dual-plane scanners at a 45° angle are employed to measure the diameter on four planes. In recent years, compact 3-axis laser head-based devices have emerged as an intriguing and advanced solution.
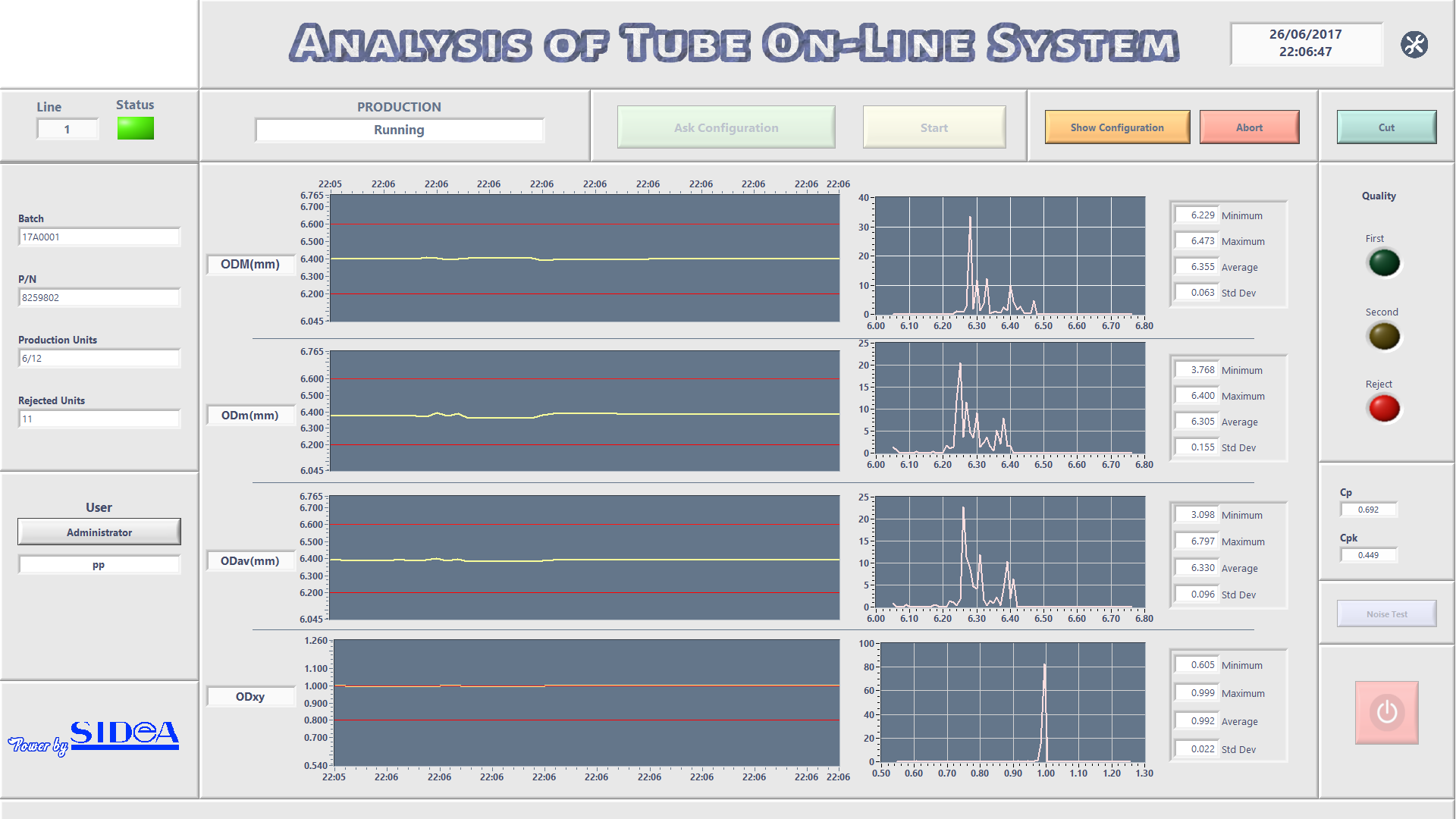
Further enhancements in processing have enabled single-scan assessments and in-line error detection. Various statistical calculation techniques are routinely used to derive an average outer diameter (OD) for feedback control and general tolerance alerts. Unlike previous systems that solely relied on averages and risked overlooking errors, single-scan systems can now compare each successive pair of scans to an average, promptly identifying errors and triggering alarms and data recording.
These advancements in measurement and control technology provide increased precision to ensure quality assurance, ensuring that small-diameter polymer tubes meet the most stringent industry standards.
Sidea Quality Control Architecture
SIDeA has developed a specific system for quality control in the production of extruded plastic pipes. The main features of the SIDeA quality control architecture include:
Online diameter monitoring
Interaction with the extrusion line
Statistical Process Control (SPC) functionality
Integration with batch processing and packaging
Industry 4.0
A universal interface module is integrated into the monitoring system for any type of connection, such as RS485, RS232, Profibus-DP, or alternatively, any industrial field like Profinet IO, EtherNet/IP, CANopen, DeviceNet, or OPC UA